Critical minerals have been placed front and centre in the new federal government’s economic plan.
This week Prime Minister Anthony Albanese emphasised the need for Australia to capitalise on its wealth of access to these resources and to move along the critical minerals value chain in order to better compete globally.
“Australia very much has a direct interest in making more things here and improving our sovereign capability,” Mr Albanese told the National Press Club on Wednesday.
“Rare earths and critical minerals are part of the National Reconstruction Fund. It’s about taking those things here, providing financing for Australian-based businesses to invest and value-add here. Why aren’t we making more batteries here – we have almost half of the world’s lithium deposits.”
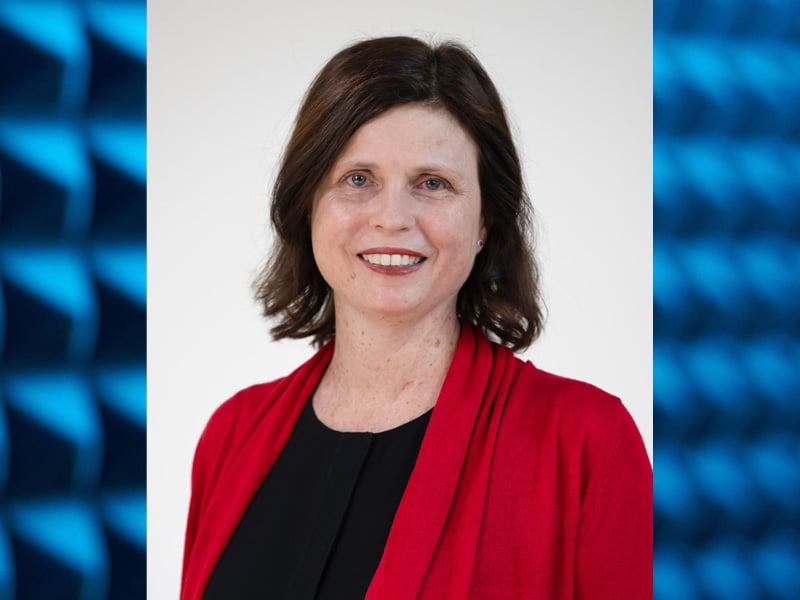
‘Critical minerals’ is a catch-all phrase to describe resources essential to the functioning of technologies and the wider economy. Australia’s critical minerals include rare earths, a group of 15 metals at the bottom of the periodic table that are used in everyday essentials such as smartphones and car batteries.
Australia boasts the world’s largest resource of rutile, zircon and tantalum, and is in the top five globally for antimony, cobalt, lithium, manganese ore, niobium, tungsten and vanadium rank.
But three-quarters of the world’s rare earths are processed in China, and Australia typically just ships these resources overseas for value to be added.
Gemaker managing director and co-founder Natalie Chapman has been involved in the rare earths industry for 15 years, and helps research organisations and Australian businesses to get their new technologies, products and services out of the lab and into use.
In this episode of the Commercial Disco podcast, Ms Chapman told InnovationAus’ James Riley that things are finally starting to move in the right direction, but more support and funding is needed.
“It’s a bit slow in the piece – I’ve been in this industry for 15 years now and for that whole time we’ve been saying we should invest in our resources and be more in the supply chain,” Ms Chapman said.
“We definitely have the knowledge, skills, expertise and IP in this country and the new government coming in has been starting to invest more in grants and R&D. It probably needs to be at a much larger magnitude.”
“These are massive chemical processing plants – we need new infrastructure to be able to do these things, and that is actually quite expensive and may need additional skills and expertise. The amount of investment needed to put into capital infrastructure is $1 billion – $2 billion for plants. The risk appetite for traditional financing institutions is not sophisticated enough to cope with that.”
Currently Australian states are often competing with each other for foreign investment in these projects. There is a significant need for a national focus going forward, Ms Chapman said.
“Overseas no-one cares if it’s New South Wales or Queensland – they’re dealing with Australia. The difficulty with projects getting investment in the past is that when you go to overseas credit agencies to try to get financing from them, the first thing they say is ‘how much has Australia put in?’.”
“If the answer is none or that they’ll put in if everyone else puts in first, then internationally they’re looking at a project and thinking, is this country serious about that project? Is it a bit dodgy? Australia’s thinking has to change — it needs to be about how many Australian dollars are in there overall.”
The federal government is currently consulting on national strategies for critical minerals and battery manufacturing, and the sector has been included in its flagship National Reconstruction Fund.
These strategies should focus on keeping these resources locally to add value, and then exporting them overseas, Ms Chapman said.
“As a country we’ve been used to the whole concept of foreign investment, and digging stuff up and sending it overseas to be processed and used en-masse,” she said.
“We haven’t in the past looked enough at downstream processing and manufacturing, and getting all the way to finished goods.”
Do you know more? Contact James Riley via Email.