Electronics manufacturers such as Entech Electronics have had to beef up their supply chain and purchasing teams to meet the challenges of a global shortage of electronic components. Yaser Darban explains what companies can do to weather the shortage.
As the world recovers from a pandemic, another threat looms for manufacturers – a global shortage of components. So when companies like Apple say that a chip shortage can cause a loss of $3 billion to $4 billion, it makes us wonder how even industry leaders didn’t foresee it.
The global chip shortage didn’t come without its warnings, which many industry leaders failed to heed.
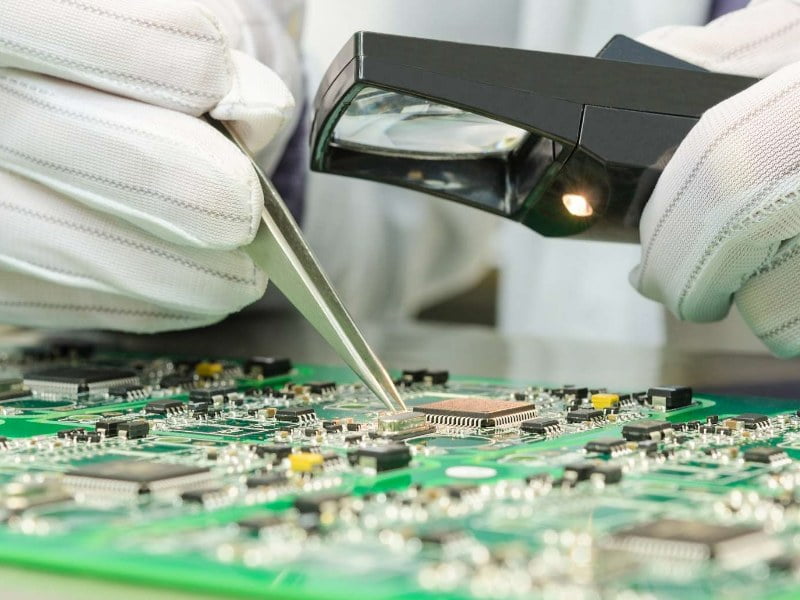
Projections say that the global chip shortage will last at least another 12 to 24 months, but there are ways in which businesses can mitigate the problem to manage the crisis better.
Practical solutions to chip shortage
We must plan actionable steps to prepare for and reduce production risk due to global components shortage.
Price is not the key element; the total value is important.
Prioritizing the total value over the price of the components will affect how your business runs. Amidst shortages, prices are going to be high.
In such a scenario, you may choose to lower your purchases. However, this strategy will affect the consistency of supply and the time to market.
It is important to be mindful of this challenge to set competitive pricing. If one associates a value with a cheaper component price, the long-term effects of this decision can be detrimental to the progress of your manufacturing business.
It is better to place the value on the end product and not on the individual prices of parts. As a manufacturing unit, better not sacrifice time, be it weeks or months, for a marginal reduction in the BOM (Bill of Materials).
Yes, by waiting for a few months, it is possible to reduce the BOM cost to some extent by design improvement. However, it also means that there are going to delays in the order. It is better to secure parts that are fixed in the design as soon as possible. Ultimately, customers will choose other suppliers who have enough inventory available.
Ordering parts early will only have a minor difference in procurement costs, but with a well-planned inventory, the production schedule will be much better. Eventually, this decision will help boost brand image, which should ideally be the real end goal of any manufacturing business.
Collaboration matters
The collaboration between the customer, designer, part supplier, and the manufacturer is essential to keep the flow of products moving and keep the business growing. When one chain breaks, it will lead to unforeseen delays and holdups.
Currently, we see that these essential components within the industry follow a closed loop. Most designers and manufacturing companies are unwilling to share their product information or BOM, fearing that it would compromise their IP.
However, if the lines of communication are open, there will be a significant shift in how these components work with each other. Professional and experienced operators can identify how to avoid compromising IP and connect clients to enablers in the supply chain network.
To navigate this situation, companies should consider sharing as much information as possible with manufacturers and/or part distributors.
If a reliable supply chain partner is not available, start looking for one that can be trusted. A connected manufacturing partner with a robust supply chain team can serve as a valuable consultant to advise on how to plan procurement and avoid shortages.
Communication is the key
Communication is the bond that keeps each part of the company in sync with each other. In a manufacturing business, it is crucial to promote the connection between supplier capabilities and customer requirements.
When creating a product, the earlier the critical suppliers are involved in the vision, the better. This process brings supplier expertise to the mix and provides businesses with essential insights into designing the product efficiently.
Another advantage is that companies will be well-versed with the supplier’s capabilities. Matching the supplier capabilities with customer demands yields the best results when it comes to manufacturing.
Besides, with the supplier’s visibility on material lead-time, planning is easier in the current shortage situation.
Everyone should get a chance to express their concerns about the product or parts of it. If there is no voice for constructive criticism or concerns, people will not contribute positively even when knowing that a certain decision would hinder the company’s progress.
In the same light, suppliers and manufacturers may have critical information or warnings for the company, urging them to plan in advance. When the industry is experiencing turbulence, suppliers/manufacturers will see it coming in advance. Hence, it is always a good idea to consider their concerns and inputs.
Planning
During the global chip shortage, one company that thought to suffer the most fared much better than its competition – again, it’s Toyota.
The automaker perfected a just-in-time supply chain strategy with a core idea to identify “what is needed when it is needed, and in the amount needed.”
According to this philosophy, many thought that Toyota wouldn’t have enough inventory to weather the chip shortage storm. However, the opposite happened.
Toyota stockpiled on semiconductors for their cars and maintenance tools before the chip shortage happened. In a recently released statement, the company said that they do not see any major short-term impact from the deficit. On the contrary, Ford expects that the chip shortage will lower its earnings by about $2.5 billion in 2021.
So, did Toyota forsake its ideology? Not exactly.
Firstly, lean manufacturing doesn’t mean that there is no room for advanced planning. Toyota adhered to just-in-time manufacturing, but as always, it showed that it learns from the past.
The automotive giant was in a similar situation during the Tsunami of 2011, where its chip suppliers couldn’t supply semiconductors due to damages. From that experience, for the coming years, Toyota kept a careful eye on supplier capabilities and trends. This practice functioned like an early warning system that showed the impending chip shortages.
During the pandemic, Toyota foresaw the effects it is going to have on the semiconductor industry. The company then took the list of the most important semiconductor components it needed to stockpile and did just that! Toyota merged just-in-time production with advanced planning, where they stocked more components if they identified an impending scarcity.
Not relying on the grey market
An efficient supply chain is possible by establishing standard processes such as supplier analysis and qualification and financial and commercial controls. This process discipline provides the ability to compare and contrast options, boosts product output, and also plays a more prominent role in the success of supply chain partners.
When this process is absent, businesses likely look forward to the grey market to compensate for the low inventory. However, this solution is more like a pain killer that subsides your pain for a short period but won’t make it go away completely.
These short-term solutions do not provide answers to why there was a shortage in the first place. Besides, grey market components may not uphold the same quality standards as the primary supplier/manufacturer.
Additionally, if the customer feels a dip in quality, it will diminish the brand image, making the short-term gain insignificant to a much more significant loss in terms of customer perception.
A few considerations can go a long way
Before the chip shortage, the usual approach for businesses was to order parts after seeing the finished design. Although it is still the right approach to design, test, validate and certify the new product before mass production, consuming more time in the current situation may now result in inadequate stock or no stock at all.
The solution is to source parts on the move. For example, businesses can avoid waiting to finish EMC testing before ordering parts since most components like the MCU or connectivity modules will likely not change at the EMC stage.
If the prototype is nearing completion, it is already known that many of the parts will not change. At this stage, it is better to move forward with ordering the critical components for production.
Minor modifications to some parts are inevitable, but waiting till perfecting the entire design will negatively impact the part availability.
While regulatory approvals and certifications are necessary, they won’t likely impact the main electronic components in the BOM. So it makes sense to order parts in advance to prevent shortage issues later down the line. It is better to consider as many alternatives as possible on each of the parts on the BOM.
As always, think long-term. When ordering parts, make sure to source enough so that you can keep the production running for the next 18-24 months.
Understanding the current shortfalls of your manufacturing business during the global chip shortage will offer you valuable insight into what you can do for the future to prevent such a scenario from happening. At the core of it, foresight, planning, and communication are the key drivers that will enable your business to overcome such a situation.
Yaser Darban is general manager, sales strategy, APAC, EU at Entech Electronics.
This story was originally published by @AuManufacturing. You can subscribe to the @AuManufacturing newsletter here.
Do you know more? Contact James Riley via Email.